The road to a self-balancing exoskeleton
This year, Project MARCH X is working on an exoskeleton that can stand independently without the use of crutches. It is an ambitious step in the ten-year history of the student team dedicated to supporting people with spinal cord injuries. The challenge lies not only in designing an innovative system, but also in ensuring that the exoskeleton is strong enough to withstand the forces that occur during use, while avoiding becoming unnecessary heavy.
To simulate these loads and to optimize the design, the engineers are collaborating with Femto Engineering. Using Simcenter 3D, they perform a FEM analysis at assembly level. The entire exoskeleton, including connections, bolts and contact surfaces, is taken into account. Analyses like these are crucial, as they validate not just individual components but also the behavior of the complete system under realistic load cases.
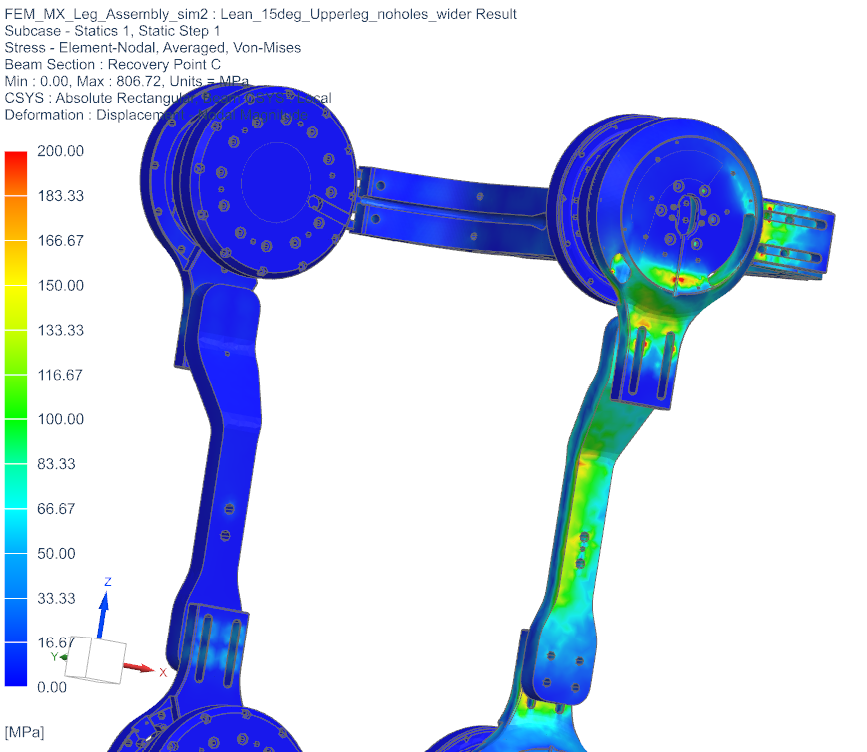
Complex simulations with expert guidance
For mechanical engineer Kira Geluk, this was her first year working with FEM software. With guidance from project engineers Maarten and Patrick at Femto Engineering, she embarked on a steep learning curve. Instead of starting with simple parts, the tight project timeline required the team to immediately tackle complex assemblies. This made it clear how critical it is to define the load cases correctly, since the results are only as good as the input. In collaboration with previous teams and other engineers within Project MARCH, various scenarios were developed, ranging from falling onto one foot to stopping abruptly while walking.
There were assumptions behind each simulation: Is the contact definition realistic? How much detail does the model need? Which parts are critical? Thanks to the weekly sessions with Femto, the process became more structured and the full FEM analysis could be used effectively for realistic design validation.
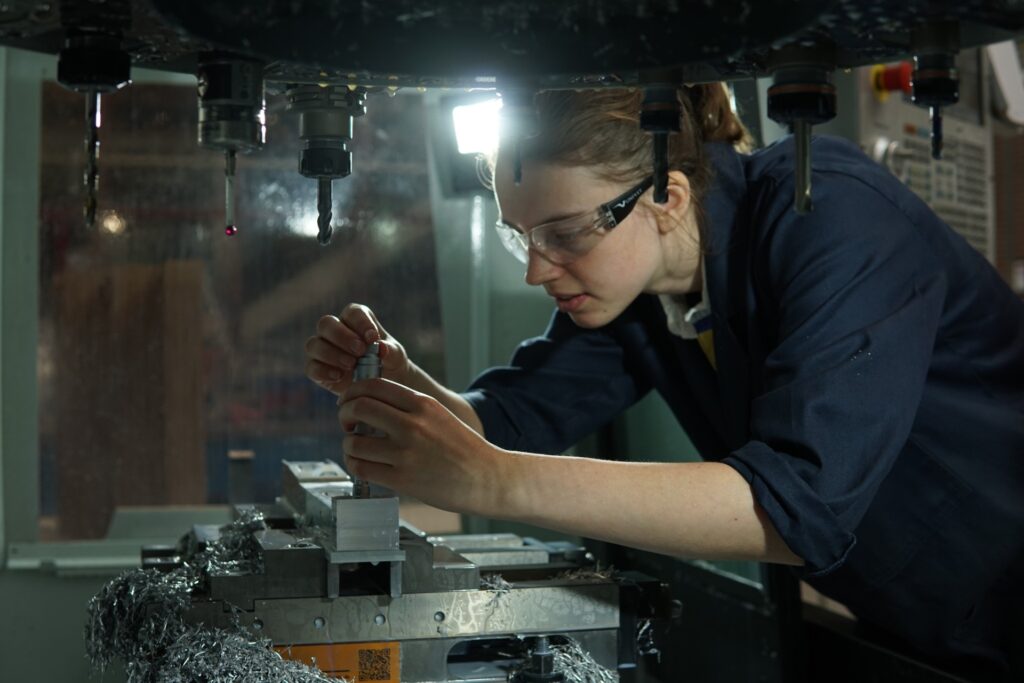
Validation and realization
The insights gained were immediately applied to iteratively redesign the mechanical components. In the end, a large part of the parts designed by the team were also produced in-house, including with CNC machines. This combination of in-depth simulation and practical realization made it possible to build a robust exoskeleton that is now ready for the testing and training phase. In this way, we are taking another step closer to independence by and with autonomous balancing exoskeletons.
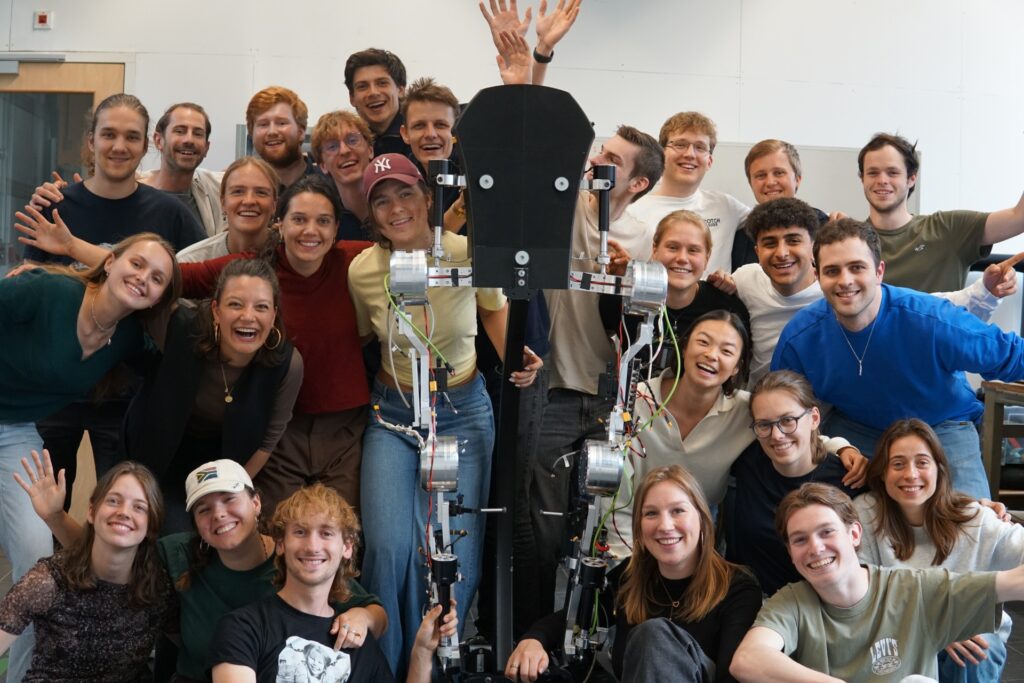
From Femto Engineering
Thank you to Project MARCH for this amazing collaboration. Want to learn more about Project MARCH? Click here to learn more.
Are you part of a student team and interested in collaborating with us? Contact us at info@femto.eu to discuss further information.